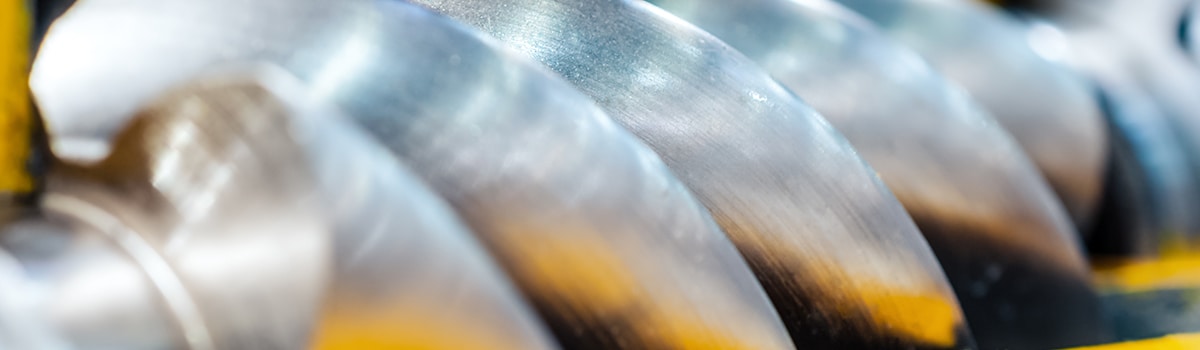
Air Compressors 101
Millions of people use air compressors every day, but if one was in front of you, could you explain how it works?
You've probably seen where and how they're used over the years, but knowing the mechanics behind how the parts work together is more applicable than you might think.
Already know the basics? Read our Ultimate Air Compressor Guide to learn which type of air compressor is perfect for your application. This article is for the gearheads, the techies, and the innately curious.
History of Air Compressors
Early humans might not have understood anatomy or physics, but they understood the potential of using forced air compressed by their lungs. By blowing on their fires, our ancestors were able to grow the flames into larger, more powerful sources of heat and energy.
Thousands of years later, the societies of the Iron and Bronze Ages had evolved to create useful tools that could be implemented on a larger scale. Metalworkers in China's Han dynasty used hand and foot-powered bellows to stoke the flames in their forges as early as the Third Century BC.
It wasn't until thousands of years had passed that an engineer named John Smeaton devised a way to compress even greater volumes of air in 1762. His invention employed a water wheel to power a moving cylinder-a piston-that compressed air in a large chamber.
Smeaton's design led to further innovations, such as John Wilkinson's development of a machine with an efficient rotating cylinder in 1776 and George Medhurst's invention of a motorized air compressor in 1799.
Since the days of wheels, belts, and metalwork, the most significant innovations in air compressors have taken place in the last 50 years. Today, the market continues to evolve to keep up with ever-increasing industrial demands.
Air Compressor Basics
The concept of compressed air is simple: when atmospheric air is stored under pressure, it creates potential energy that can be held inside a tank until it's needed. Just like a balloon being released, when the pressurized air is released, the potential energy is converted into usable kinetic (motion) energy.
By harnessing that transfer of energy through pneumatic (air) tools, we are able to work on tasks that were before impossible.
What is Air Displacement?
The core of how air compressors work is boiled down to two methods of air displacement.
In order to compress air, the internal components of a compressor must move or change position to mechanically force the air through the chamber where it is compressed and stored until use.
Positive Displacement is the method that most compressors use. Air is pulled into a
chamber that opens and closes, where the internal parts reduce the volume of the chamber and compress the air. Once the cycle is complete, the air is pushed through the chamber and into a storage tank where it waits to be used.
Piston, rotary-screw, and scroll-type air compressors all use positive displacement to compress and store air.
Dynamic (nonpositive) Displacement uses rotating blades on an impeller to pull air into the chamber, where the energy from the motion of the blades builds air pressure. Often used with turbocompressors, this method of air compression produces huge volumes of compressed air quickly, and this technology is commonly found in cars that use turbochargers.
Air compressors that utilize this method of displacement are often reserved for commercial/industrial applications when large volume flow rates and constant pressure are needed.
What Drives an Air Compressor?
Compressor drives are most commonly direct-drive or belt-driven systems. In a belt-driven system, as the motor turns, the belt turns with it, thus activating the pump in the system. This is the more economical option and is widely used across all compressor types because the belts can be adjusted to change with air demands.
In a direct-drive system, the motor attaches directly to the crankshaft of the compressor, allowing for smaller designs and fewer maintenance requirements. Although not much adjustment can be made to these drive systems, they are more efficient because less power is lost in the transfer of power to the crankshaft.
Another benefit of direct drive is the ability to provide compressed air without needing to fill a storage tank first, like using a DC compressor for off-roading.
The Mechanics of an Air Compressor
Depending on the type of air compressor, basic air compression requires an electric-powered motor, a pump with an internal mechanism to compress the air, an inlet/outlet valve to draw in and release air, and-in most cases-an air storage tank.
Air is drawn into the compressor where the internal components reduce the volume of the air by creating a vacuum, which drives the pressure of the air up as it is pushed into a holding tank. Once the maximum pressure is reached inside the tank, the duty cycle is complete, and the compressor shuts off until the pressure falls below a set threshold. Positive displacement air compressors do this in different ways: by using pistons, screws, and scrolls.
Reciprocating Piston Compressors
Piston-type air compressors operate similarly to the combustion engine in your car. When the crankshaft's rod raises the piston inside the cylinder, it forces air into the compression chamber. This decreases the air volume (thus increasing air pressure) as the crankshaft drives the piston closed and pushes the compressed air into a storage tank. Then, the piston opens again to draw more air in.
Piston compressors can achieve a full compression cycle (stroke) in 1 or 2 stages:
- Single-stage:
The compressor uses a piston to compress the air in one stroke (a full rotation of the crankshaft that drives the piston a full motion). In some single-stage models, multiple pistons are used to divide up the work and can operate at lower RPMs and decibels. - Two-stage:
The compressor compresses air in one stroke using one piston before moving that pressurized air to a smaller cylinder for the second stroke from a second piston. This doubles the air pressure stored in the tank.
Piston compressors are notorious for being louder because the internal components rub together and create friction. However, advancing technology is improving the way they operate by introducing dual and multi-piston, single-stage models that use up to 4 pistons inside the pump.
By using multiple pistons, the work of a single piston can be divided up, extending the life of the unit and achieving a supremely quiet air compressor.
Rotary-Screw Compressors
Instead of using a piston, rotary screw compressors squeeze air between two helically-opposed screws that don't touch, reducing noise and maintenance.
These compressors were created for heavy-duty applications that require high power during extended periods and are ideal for maximum air intake and production.
Rotary screw compressors are oil-sealed and have fewer moving parts, so they operate more quietly and require less maintenance because of the design.
Scroll Compressors
The third type of positive displacement compressor, scroll compressors, are known for their highly efficient, oil-free, and quiet operation. Similar to rotary compressors, the scroll design uses two interwoven metal pieces that work together but don't touch to create a vacuum.
Two spiral-shaped circular pieces rotate around one another to compress incoming air. One scroll is fixed in place and doesn't move, and the other fits inside the stationary scroll and moves in a tight circular motion without rotating.
Lubrication
Just like your car uses oil, air compressors need lubrication to continue running smoothly over time.
Lubricated air compressors use oil to reduce wear and friction on their moving parts. In the case of piston compressors, the oil is applied to the system in one of two ways:
- Splash lubrication: a dipper attached to the piston rod dips into an oil-filled trough and splashes the oil onto the piston and cylinder.
- Pressure lubrication: A pump sends oil through passages drilled inside the compressor, applying the oil to specific parts. Pressure-lubricated systems are generally more expensive, but the directed flow of oil keeps them operating longer than their splash-lubricated counterparts.
Non-lubricated compressors are also referred to as oil-less or oil-free because their parts are coated in special chemicals or materials like Teflon to reduce friction instead of conventional oil. The solution here is permanently-lubricated components. The drawback of non-lubricated compressors is that they heat up faster, and aren't the best option for heavy-work environments.
Most oil-less air compressors are used in industries where clean air is required for manufacturing, such as in the food, beverage, and electronics industries. For example, scroll compressors are used in the dental industry because of their continuous clean and quiet operation.
Measuring Power
When it comes to sizing an air compressor for airflow and air volume, there are two criteria professionals use to determine if an air compressor can properly handle an application and determine the kinds of tools that will be compatible with your air compressor.
1. Pressure is the amount of force applied to the surface of a given area. For compressed air and gases, this force is measured in pounds-force per square inch, or PSI. The higher the PSI rating, the greater the amount of force applied to the air within a compressor.
2. Airflow volume is a measure of the rate at which air can move into a compression cylinder and the machine can compress it. For air compressors, the volume of air is measured in
cubic feet per minute, or CFM. The higher the CFM value, the greater the volume of air a compressor can generate.
An easy way to understand how pressure and volume work together is to think of a garden hose. By putting your thumb over part of the hose opening, the same amount of water is forced through a smaller space, thus increasing pressure at a constant flow. By increasing the amount of water coming through the hose, more work can be done faster.
New Innovations in Air Compressors
Air compressor technology used to be expensive to produce and used a lot of energy to power, making it only affordable for the commercial industry. Even today, commercial air compressors still use significant energy.
As a general rule, you can expect to spend about $500 per horsepower (HP), per year using an industrial air compressor in continuous use. For example, a 10 HP compressor will generally equal $5,000 in operations costs per year.
In efforts to bring down costs and increase efficiency, new technologies are being introduced each year that innovate the possibilities and capability of compressed air. Engineers are finding ways to make compressors more powerful and energy-efficient, such as through variable speed drives (VSD) that allow the compressor to change motor speeds and voltage as air demands change, saving energy and money.
Even newer is the variable frequency drive (VFD) technology that takes this concept a step further. This technology allows the compressor to control the motor speed and torque by alternating from A/C to D/C power and controlling the input frequency and voltage, meaning the most efficient power usage available on the market.
Other innovations, including changes to the rotor speeds of rotary screw compressors, the use of water as a lubricant in place of oil, and the incorporation of remote monitoring systems all promise to deliver even greater improvements to efficiency in the near future.
The short of it is: air compressors aren't going to disappear, but instead continue to allow millions of people to get more work done faster and more effectively.
Air Compressor Buyer's Guide Navigation
Ultimate Compressor Guide |Air Compressors 101| For Homeowners |For Contractors |Stationary Compressors |Portable Compressors| Quiet Compressors |Energy Efficiency |Air Treatment Systems |Air Filters 101 |Air Tools 101 |