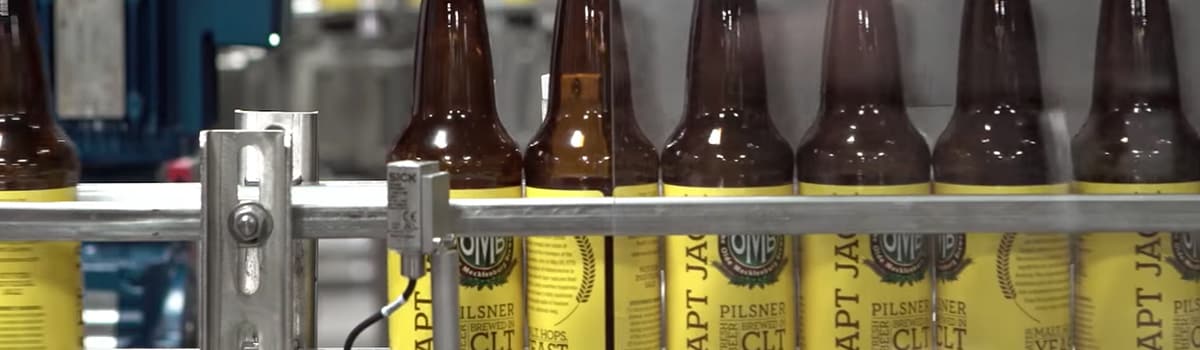
Brewery Air Compressor Buyer's Guide
Craft brewing is equal parts art and science and within each craft beer lies an unmistakable personal characteristic of the master brewer.
Extreme care and thought go into every aspect of the brewing process, each making a quantifiable mark on the final product. From concept to creation, no detail is too minute to ignore and the compressed air system is no exception.
“Invention, my friends, is 93% perspiration, 6% electricity, 4% evaporation, and 2% butterscotch ripple.”
- Willie Wonka
Types of Air Compressors for Brewing
One brewery may use compressed air just for washing kegs while another will need continuous air to power bottling equipment. The type of air compressor you choose depends on the size and needs of your operation.
Reciprocating
Reciprocating compressors work just like a car's engine, except without the combustion. They use rotating pistons that generate a lot of heat and noise.
Heat that can wreak havoc on equipment and even with driers and filters, allow oil and moisture to leak into the lines, or worse, into the product. Therefore, reciprocating compressors are regulated to cleaning tasks like keg washing and small pneumatic tools.
Reciprocating compressors are popular among small microbreweries because they offer an affordable up-front cost. However, the energy cost in one year may exceed the cost of the compressor and fail more frequently than other types, so they're not as economical as they first appear.
Still, the best reciprocating compressors for a home brewer and micro-brewery will be an oil-free, quiet type featuring a dual-piston design that operates at lower RPMs and temperatures.
In most cases, duplex compressors will last around 4 times longer than a standard compressor. For applications requiring a higher pressure (PSI) or capacity (CFM), look for a two-stage duplex air compressor.
Rotary Screw
Rotary screw compressors are extremely versatile machines. Similar in design to a turbocharger, they are inherently quieter and produce cooler, more robust air than reciprocating compressors. They are also intended for extended use and variable-speed rotary screw compressors are much more energy efficient adding savings right to your bottom line.
By far the most popular choice among serious craft brewers, continuous-duty rotary screw compressors are uncompromising workhorses that can wash kegs and power brewing equipment.
Oil-Free Scroll
Scroll air compressors are mainstays in pharmaceutical, food/beverage, lab, and production facilities due to their supremely efficient, whisper-quiet operation that delivers continuous clean air.
Brewers benefit from the oil-free design because they don't have to worry about pressure drop-off associated with oil filters on other types of compressors. Scroll compressors can also be installed almost anywhere due to their low noise level without worrying about disturbing the brew-pub up front.
Air-Powered Brew Equipment
Commercial and craft breweries alike depend on compressed air for powering continuous-duty machines (like Meheen) for bottling, labeling, filling, and carbonating. These machines require a very precise amount of clean, oil-free air and are very expensive to own and repair.
Aeration
Aeration is an essential process of introducing oxygen to the yeast cultures throughout the fermentation process.
Oil-free compressors are ideal because they don't risk contaminating your malty masterpiece with oil - affecting the quality and the taste of the resulting beverage. Who knows, oil-free air may even make its way into a revised version of the Reinheitsgebot!
Clarifying
Several prominent microbreweries also use compressed air to power machinery during the clarifying process. After primary fermentation, many of the brewery’s beers are clarified using a pressure-driven centrifuge that removes heavier solids and results in cleaner, clearer finished product.
Bottling
Bottling is one of the most common uses for air compressors in home breweries and smaller commercial operations. Pressurized air is essential for moving beer from the conditioning tank to the bottle, and for keeping lines clean and free of water.
Bottling uses a lot of air, so getting the right unit that can continuously handle around 90 PSI will pay off. If you select an undersized or non-continuous rated unit, it will most likely get hot and start spewing oil into the lines. Even with a water trap, oil filters, and water filters, contamination will still get through pneumatic lines and wreak havoc on your equipment.
Cleaning and Maintenance
You spend countless hours researching and pouring over decisions like what malts, hops, and yeast strains to use in your next award-winning Imperial Stout and nothing can be worse than to find the entire batch ruined from contamination. Cleaning brew kettles, fermentation tanks, bottles, and kegs are all necessary chores for the fun part: making awesome beer. It's how you clean that makes a difference. To avoid spoilage, you want to avoid using contaminated air at all costs.
Air compressors can be used to power cleaning tools such as pressure washers which are essential for maintaining a clean and sanitary operation. Many breweries will also use air-powered tools for regular maintenance and installation of new equipment.
Clean Air = Clean Beer
No matter what size the operation, you will want an oil-free air compressor that is UL-listed, comes with an ASME-certified tank and uses the right combination of air treatment accessories to produce the most contaminant-free air possible.
But, if you're still using an oil-lubricated compressor, you'll need to incorporate refrigerated dryers and in-line air filters to remove moisture, oil, and other airborne contaminants.
Whether you are a large-scale craft brewery or a microbrewery, choosing the right air compressor and accessories will go a long way to protect your investment and the award-winning beer you create.
The experts at Air Compressors Direct are here to help you develop a complete compressed air solution, providing you with the best selection and pricing delivered right to your door.
NEXT: How an Air-Treatment System Works