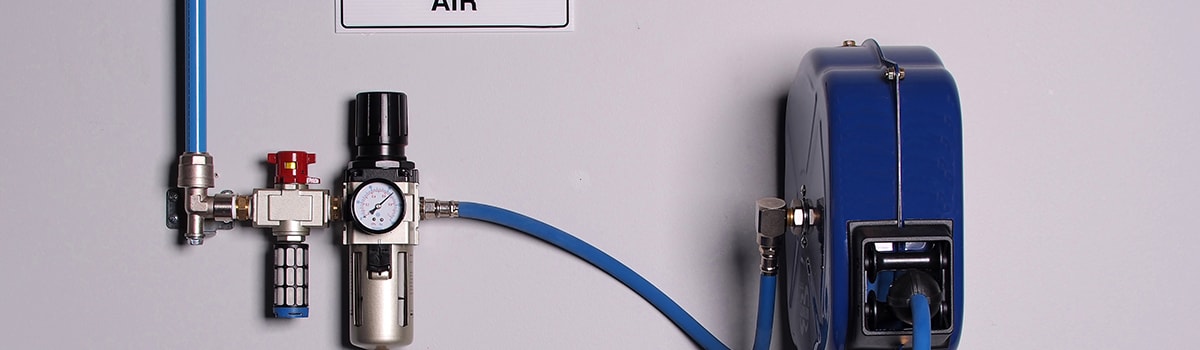
How to Maintain an Air Compressor
Air compressors are a major investment, and keeping yours running in top condition can save you loads of money over the compressor's life.
This article features a preventative maintenance checklist and a full servicing checklist to refer to while performing maintenance on your air compressor.
Before Getting Started - Tips and Advice
These are the most important things you can do before performing service or maintenance on your air compressor:
1. Read Your Owner's Manual—Before starting any maintenance on a compressor, you should always check the owner's manual. It has specific information unique to your compressor that will ensure that it is properly maintained. Even though it's the most obvious advice and is often ignored, it's the most crucial step.
2. Get Familiar with Your Air Compressor—It pays to be familiar with what the gauge readings should be on your compressor. If you do, you'll know when they are outside of the normal spectrum. Write down the readings daily and record things like oil temperature and pressure, motor amps, and discharge pressure. Doing this is the first step to conducting an air compressor audit designed to save you money. Always watch and listen for unusual sounds, overheating, excessive vibrations, or slipping belts. If something seems abnormal, it may require fixing. Always investigate the causes and fix them before it gets worse or causes more serious damage.
3. Stock Up on the Essentials—Keep a stockpile of basic supplies for maintaining your compressor. If they're not available, you're less likely to keep up with proper maintenance. Keep filters, extra seals, oil, and other maintenance supplies handy so you can change them out and repair problems on the spot. Better yet, have a maintenance kit on hand to service everything at once during full servicing.
Plus, many manufacturers offer extended warranties if the end-user purchases a maintenance kit annually because it ensures that the compressors are properly maintained. Extended warranties can range from 1-3 years for most manufacturers, and in some cases like EMAX, a potential lifetime warranty.
4. You Can't Maintain Too Much—When you think of maintenance, most people do the bare minimum. For most compressor systems, the minimum may keep the compressor operational, but you need to do more to keep it running efficiently. More important than regular servicing is implementing a preventative maintenance schedule to happen between service dates. See our checklists below for action items for each type of maintenance.
Air Compressor Maintenance Checklist (Servicing)
Below is a checklist of things that you should check every time you maintain your air compressor. Typically, this relies on operating hours, so consult your owner's manual to see specific maintenance schedules.
- Check the Oil—This is very important for any engine (large or small). If your air compressor takes oil, make sure you check it before you start it up each time. If the oil is low, you could find yourself doing serious damage to the compressor. Whenever the oil is low, top it off. Every compressor has a different operating hour schedule, but when it is reached you need to drain out all of the oil and replace it with fresh, clean oil. Check the manual for details.
Remove Moisture and Contaminants—Filters, dryers, oil separators, and even the air tanks collect water, oil, and other contaminants from the air. The only way these components can operate efficiently is if you drain the waste from them. It should be done every time you've finished using the air compressor but needs to be inspected closely during maintenance. Periodically check that the drains are all functioning correctly. If any of the drains have test buttons, use them. You can also watch the filters closely to ensure they're filling and dumping properly on their own. If your drain features a bypass, you should open it and look for condensate that could be stuck upstream behind a blocked line.
- Replace the Air Filter(s)—Frequently check all of your filters, and change them if there's heavy build-up. If you rarely use your air compressor, change the air filter every 3-6 months for optimal performance. If your air filter is dirty, your air compressor will work much harder to do its job. And even worse, you'll run the risk of contaminating the compressor.
- Replace the Separator Element—The separator element prevents excessive use of oil. You may not want to pay for a replacement separator, but it's honestly cheaper than the rise in energy costs over time due to a drop in separator pressure. For every 2 PSI the separator pressure drops, your energy costs can increase by 1 percent. Periodically replacing your separator element will keep your compressor healthy and reduce how much you're spending on energy costs.
- Clean the Fuel Tank—If you've got an oiled compressor, you'll need to clean the fuel tank during servicing to ensure it remains clear of gunk and contaminants to continue running effectively.
- Test Safety Shutdown Features—At a minimum, this should be done each time a compressor is fully serviced. Run through your company's safety procedure and follow protocol to ensure the compressor will operate correctly according to the plan.
Preventative Maintenance Checklist
Following these suggestions below will help you maintain a preventative maintenance schedule that will ensure a long life for your compressor. Preventative checks should be done periodically between full scheduled services on your compressor but can be done as often as needed. Remember, preventative maintenance is designed to catch and fix problems before they become serious. Generally, we recommend going through this list bi-weekly or monthly to make sure nothing goes unnoticed long.
- Check for Leaks Often—As much as 25-percent of compressed air that is generated can be lost through a leak. So check for leaks often, because they will significantly reduce your compressor's output and efficiency. If you're not sure how to detect a leak, you can use an ultrasonic leak detector. An even cheaper method is the liquid soap and water (bubble) test. Air leaks will show up through bubbles at the connectors if a leak is present. The most common areas that problems are detected are control lines and fittings, clamps and connectors, valves, safety relief valves, piping, pressure gauge connections, and flexible joint packing.
- Drain Moisture After Every Use—As stated above, moisture is the worst enemy of an air compressor. All moisture should be expelled from the system after every use. Follow the relevant instruction manuals to drain properly.
- Regulate the Temperature—Maintaining a proper operating temperature will help manage your compressor's efficiency, and following all of the advice listed above, you'll be more successful. However, to regulate the compressor temperature accurately, you'll need to know what that temperature should ideally be. Reference your owner's manual to find the recommended operating temperature for your unit, and keep it at or around that temperature.
- Keep Your Compressor Clean—As with any kind of power equipment or machinery, cleanliness is always a key factor in maintaining efficiency and extending the unit's life. Keeping your compressor clean and ensuring it's always properly sealed will help in managing temperature and smoother operation. A dirty compressor can equal a damaged compressor. You should never allow your compressor to have oil leaks. Do not allow dust to accumulate on the pump, motor, or cooling fin area. Excessive dust buildup will prevent heat from being properly ventilated.
- Keep Intake Vents Clean—This one should be simple enough. Periodically check the intake vents and make sure they are clean and clear of any dust and debris that could prevent air from being exhausted correctly.
- Clean Filters Often—Like the intake vents, make sure the filters being used are kept clean and checked often to ensure they are working properly.
- Check Hoses and Fasteners—Periodically check all hoses, connections, and tighten fasteners everywhere on the compressed air system. Doing so allows someone to inspect all joining components in your system to ensure there are no leaks, rusted out fasteners, loose clamps or valves, etc.
- Clean Heat Exchangers—Cleaning the heat exchangers and making sure they are operating correctly will lengthen the life of your compressor system.
- Check Belts—Belts often go unnoticed until they begin making noises. After all, the squeaky wheel gets the grease. Don't forget to check your belts from time to time to ensure they are not loose, cracked, or overheat while in use. Don't forget to check the guard while you're at it.
Why Maintenance is Important
It should go without saying, but there are countless reasons why you should properly maintain your compressor during its entire lifespan. Some of the most important reasons are:
- Optimal operating efficiency at all times
- Prevents wasting money on leaks, damaged components, etc.
- Safety for you and/or employees during operation
- Increases the lifetime of your investment (dollars go further)
You've spent a great deal on your compressed air system, so why wouldn't you want to take steps to keep it healthy, running efficiently, and alive as long as possible? It's like they say, "An ounce of prevention is worth a pound of cure." In all examples, it's better to spend a little on maintenance over time than to buy a new compressor that died earlier than it should have.